New Energy Vehicle Connectors: The Core Driver Empowering Architectural Upgrades

In the wave of transformation towards electrification, connectivity, and intelligence in the automotive industry, connectors, as the “neural hubs” of electronic systems, are undergoing unprecedented innovation. From traditional vehicles to new energy vehicles (NEVs), connectors have not only undergone qualitative changes in quantity and function but have also become a key force driving the upgrading of vehicle architectures.
I. NEV Connectors: Functional Reconstruction Behind the Surge in Quantity
Traditional fuel-powered vehicles require approximately 600 connectors per vehicle. However, due to the exploding demand for power transmission and signal interaction in NEVs, this number has risen to 800-1000, covering all scenarios such as high-voltage power systems, low-voltage control systems, and intelligent driving sensors.
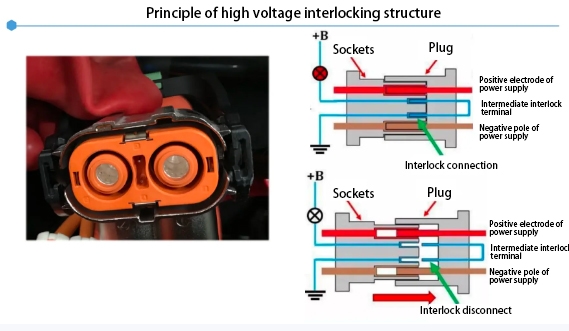
Principle-of-high-voltage-interlocking-structure
Behind the growth in quantity lies a comprehensive upgrade in functionality. NEVs have moved away from engine power systems dominated by low-voltage control to high-voltage power architectures, directly transforming connectors from “single signal/low-voltage transmission” to a composite function of “high-voltage power + high-speed signal” transmission.
II. High-Voltage vs. Low-Voltage Connectors: Technical Differentiation Driven by Diverse Needs
The transformation of NEV electrical architectures has led high-voltage and low-voltage connectors down distinct technical paths.
Low-Voltage Connectors: Stabilizers of Basic Architecture
Although high-voltage systems are the core of NEVs, low-voltage connectors still play a crucial role in connecting large-scale infrastructure such as body control, sensors, and in-vehicle entertainment systems. They ensure the stable operation of basic functions like door control, lighting adjustment, and information display, serving as the backbone of the vehicle’s “soft power.”
High-Voltage Connectors: Main Force in the High-Voltage Era
As NEV high-voltage platforms advance toward 800V, high-voltage connectors have become the focus of technological breakthroughs. Compared to low-voltage products, they must meet stringent requirements such as heat resistance, voltage resistance, current-carrying capacity, and electromagnetic compatibility (EMC). For example, in 800V high-voltage systems, connectors must withstand higher instantaneous voltage surges while controlling temperature rise during continuous high-current transmission to ensure driving safety.
Through multiple iterations, the performance of high-voltage connectors has continuously improved: ultra-high current busbar solutions optimize current-carrying capacity, while lightweight designs indirectly enhance NEV range by reducing vehicle weight—key pillars of high-voltage architecture upgrades.
III. Signal Connectors: Dual Challenges of High-Speed Transmission and EMC
In the era of intelligent mobility, NEVs’ demand for data transmission is growing exponentially. Autonomous driving LiDAR, millimeter-wave radar, and V2X communication all rely on signal connectors for high-speed, stable data interaction.
This requires signal connectors (such as coaxial and differential transmission connectors) to have greater bandwidth to support real-time transmission of massive data. Meanwhile, electromagnetic interference (EMI) in all-electric, high-power environments poses a critical challenge: ensuring signal links remain unaffected by electromagnetic fields during high-speed transmission has become a core test of connector reliability.
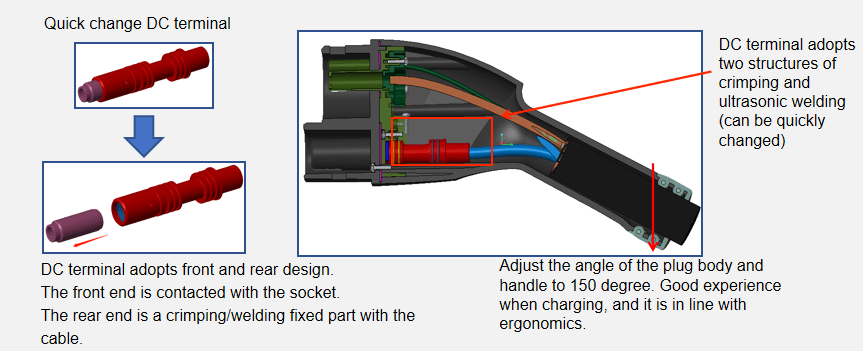
NEV fast-charging connector – high-current transmission and liquid-cooled heat dissipation design
IV. NEV Energy-Supplementing Connections: Technological Game Between Fast Charging and Battery Swapping
The uniqueness of high-voltage connections in energy supplementation has made charging and battery-swapping connectors critical links in the NEV “energy chain.”
Battery-Swapping Connectors: Tolerance Priority
Battery swapping places relatively focused demands on connectors: they need sufficient floating compensation capability to accommodate potential tolerances during vehicle-battery separation. The core lies in “compatibility with tolerances” rather than extreme power performance.
Fast-Charging Connectors: Extreme Challenges Under High Voltage and Current
As fast-charging technology evolves toward “300km range in 10 minutes,” charging connectors face unprecedented challenges in current carrying and temperature rise. To support high voltage (e.g., 800V) and high current (over 400A) transmission, connector materials (e.g., high-temperature-resistant insulating materials) and structural designs (e.g., liquid-cooled heat dissipation channels) must break traditional frameworks. For instance, some fast-charging connectors incorporate built-in liquid cooling systems, enabling continuous current-carrying capacity exceeding 600A while controlling temperature rise within 20°C.
Conclusion: Connectors as the “Invisible Cornerstone” of NEV Architectural Upgrades
From low voltage to high voltage, from signals to power, and from in-vehicle systems to energy supplementation, connector innovation runs through the entire chain of NEV architectural upgrades. Their performance optimization directly impacts vehicle safety, range, and intelligence, and even determines the pace of NEVs advancing toward higher voltage platforms, faster energy supplementation, and deeper intelligence. In the future, as solid-state batteries and L4 autonomous driving mature, connectors will face greater challenges and unlock greater innovation potential.